The Rough
The whole process begins with the rough crystal. Crystals come in many different shapes and forms. Some are still in their “crystal habit” (the natural form in which a particular gem mineral develops) others have been broken by the mining process or by nature itself with the twisting of the rock in which it formed. Others still, are alluvial and carry the appearance of water worn pebbles.
Various Shapes of Rough. Recent rough cystals seen in our offices. From left - Alluvial Malaia Garnet, Random shapes of Tanzanite and Tsavorite and a Tourmaline in its crystal habit.
Less rare gems, produced in quantity and smaller sizes are often cut as calibrations - standard sizes. In the case of these cuts, the principal consideration is a uniform size - an 8 x 6 oval for example. However, with fine, rare gemstones, the shape of the rough generally dictates the eventual shape of the finished piece, rather than any allusion to a standard size. This is because fine gemstones are very rare and expensive and a cutter will try to maximize the yield he gains from a piece of rough in order to minimize loss of weight - weight is money.
Hence, a short stubby crystal may lend itself best to a round cut whilst a long tourmaline pencil would almost certainly be cut as an emerald cut as this would be the shape that incurs the least loss. Balancing the need to maintain weight and the importance of good proportions to create good light return is the cutter’s eternal challenge. Stones which are cut purely to maintain weight and do not take into consideration symmetry, beauty and brilliance are not considered to be top grade – and a bad cut can ruin a very good piece of rough.
The process of cutting fine rough into a scintillating finished gemstone is called faceting. This is a very skilled process where a cutter places a number of carefully placed facets (or faces) onto the table and pavilion of a gemstone. The steps taken to achieve this are considered below.
Planning the Cut
This is a very important step. The cutter will consider the shape of the rough and the inclusions within it. Once he has determined the “lie of the land” he must decide how he will orient the cut – where the table will sit and where the pavilion will be. Many things are taken into consideration here – any bad inclusions must be removed, color banding and zoning, if present, will affect the orientation of the table as will the actual shape of the piece.
Once the cutter has examined the piece thoroughly he will begin to clean the stone up. If a piece requires slicing it will be done with a special machine. Otherwise included areas are ground off with a special lap.
Preshaping & Dopping
Next comes preshaping – this is a skilled art. It is done “freehand” – the cutter holds the rough stone in his hand and grinds it using a spinning wheel called a “lap” primed with diamond powder. This will produce the very basic shape of the cut.
The preshaped piece of rough is now attached to a special metal rod called a dop. Special dopping wax is used to do this. The dopped rod is then connected to a handheld faceter.
From Rough to Dopped. From left - A rough crystal being examined before cutting. Middle Pic - Preshaping on a specialized lap. Right - Preshaped stone is "dopped" - placed on a dopping stick with the aid of special gem cutting wax.
Faceting
This is where the real magic is performed. Hundreds of tiny faces or “facets” are placed on the table and pavilion of the preshaped rough. This is an incredibly skilled and specialized talent which takes many years to perfect – experienced master cutters are a cherished breed.
The grinding lap is removed from the machine and a faceting lap is now used which is a much finer lap primed with very fine diamond powder. The facets are placed on the stone at extremely precise angles. The timing and skill involved here are incredible.
Using the hand held faceter, the cutter uses the Height, Angle, Index triangle to place each individual facet separately on the crown and pavilion. Height will control the depth to which each facet is cut, angle controls the plane on which the facets are cut and the index controls the placement of facets around the shape.
Rough to cut. A Rough Tourmaline pencil in its “crystal habit” lends itself well to an emerald cut (Octagon). The emerald cut maximizes weight retention where another cut would incur unnecessary weight loss.
The crown and pavilion are essentially cut to form a lens and reflector. They gather and focus the light, then reflect it back at the eye. The crown facets form the lens, gathering the light from all directions and focusing it on the pavilion which becomes the reflector, bouncing light around inside the stone and then back upwards via the crown and out to the eye.
Faceting and Polishing. From left - Preshaped Tsavorite added to the hand held faceter. Middle Pic - A preshaped Tsavorite beginning the skilled, long process of forming the table facets on a special lap primed with Diamond Powder. Right - Placing the pavilion facets.
However, the same angles are not used for every gemstone. Different minerals have different requirements and a cutter must be aware of these. This is because different gems have different critical angles. To explain - the angles used for each facet denote the final result achieved, in that they affect the brilliance and reflection a gemstone is capable of. Each facet’s angles must be adjusted to maximize its optical performance.
The angles used will vary based on the refractive index (RI) of the gem material and all gems have different RI’s. Hence, when light passes through a gem and hits a polished facet, the minimum angle possible for the facet to reflect the light back into the gemstone is called the critical angle. If the pavilion of a gemstone is cut too deep or too shallow the light ray will hit the facet outside the critical angle and the light will escape outside of the stone. This is called unplanned light leakage.
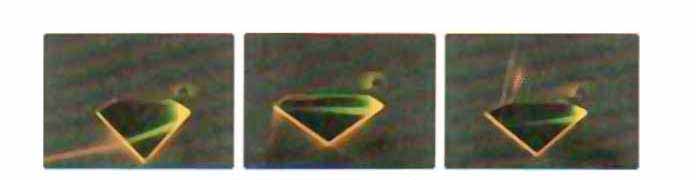
Source : GIA, Colored Stones, Asnm 135 pg 3g. The photograph shows plastic representations illustrating the pavilion’s affect on light return showing light (represented by faint orange red lines, leaking out the sides through a deep pavilion (left) and a shallow one (center). In the optically efficient pavilion at right, light leaves through the crown.
Light Leakage
Stones with light leakage commonly display a “window” demonstrated in the picture below – a dull, unreflective area which severely compromises the stone’s beauty. This is well illustrated in the image below depicting a windowed Tanzanite oval next to a well cut piece.
Two Tanzanite ovals of equal quality showing how a window can affect beauty and light return. Left : well cut Tanzanite with no window Right : Tanzanite cut too shallow with large window. The pavilion is cut outside the critical angle causing light leakage
Polishing
This is the final stage. The cutter will use a special polishing lap which is even finer than the faceting lap. It is also primed with very fine diamond powder. Each facet is then polished individually to a high sheen, giving the stone a fine luster.